Tecnica Group: «Il nostro piano per riciclare 300 mila scarponi»
Uno dei gioielli dello Sportsystem trevigiano lancia il progetto di un nuovo impianto industriale per recuperare l’attrezzatura da sci, dopo il successo di “Recycle your boots”. Zanatta: «Sarà un progetto aperto a tutti»
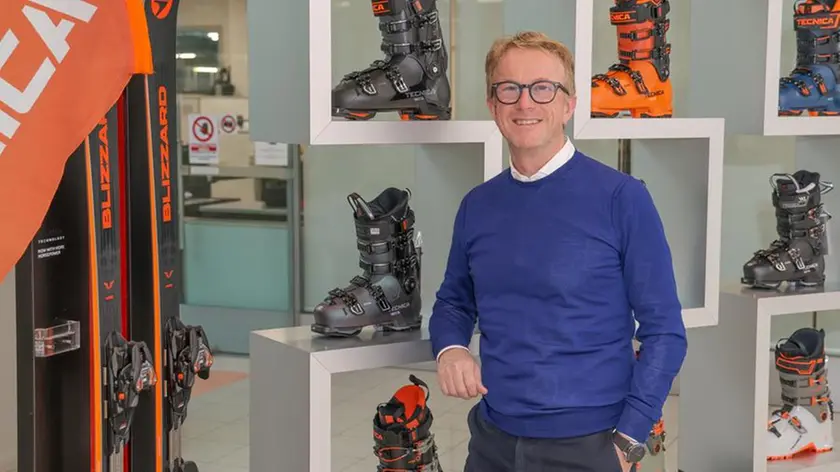
«Il nostro distretto dello Sportsystem è già un’eccellenza a livello mondiale per la produzione di articoli sportivi, con tanti marchi conosciuti e apprezzati ovunque. Ora abbiamo la possibilità di diventare un punto di riferimento anche per il riciclo dei materiali utilizzati nelle attrezzature, soprattutto se riusciremo a fare sistema e muoverci insieme».
Alberto Zanatta, presidente di Tecnica Group, parla nell’atrio della sede dell’azienda, a Giavera del Montello. Alle sue spalle c’è un espositore con alcuni degli sci e degli scarponi che vengono concepiti qui, dall’altra i più glamour tra i Moon Boot, icona dell’abbigliamento che ogni anno vengono prodotti in 700 mila paia. Quattro anni fa, era il periodo del Covid, Tecnica ha dato vita a un progetto che prima ha dimostrato la possibilità di riciclare gran parte delle plastiche degli scarponi e, poi, ha iniziato a introdurre nei suoi prodotti i materiali a cui viene data nuova vita.
I risultati sono già notevoli, con quasi 30 mila paia di scarponi riciclati, ma ora il gruppo sta lavorando a un salto di qualità. I prossimi passi, infatti, dovrebbero portare alla realizzazione nei pressi della storica sede di Giavera di un nuovo impianto per il riciclo, una prima assoluta a livello mondiale: «Abbiamo individuato l’area e predisposto il layout, vedremo se sarà possibile passare alla fase operativa», dice Zanatta.
Presidente, com’è iniziato questo progetto?
«Nel periodo del Covid, quando l’attività ordinaria era rallentata e avevamo un po’ di tempo in più per fermarci a riflettere, un collaboratore mi ha chiesto se potevamo investire 25 mila euro per un progetto su come riciclare gli scarponi da sci. Ci ho pensato e ho risposto di sì, che per un’idea come questa ero disposto anche a perdere una cifra del genere».
Poi che cosa è accaduto?
«Uno scarpone da sci è un oggetto molto complesso, che al suo interno arriva a contenere 100 materiali diversi, tutti con caratteristiche tecniche tali da garantire le prestazioni necessarie. Grazie al lavoro del nostro team e alla collaborazione con il dipartimento di Ingegneria industriale dell’università di Padova, abbiamo capito che era possibile riutilizzare buona parte delle plastiche con costi sostenibili. Abbiamo elaborato il progetto “Recycle your boots” e ci siamo candidati per i fondi europei Life, vincendo un bando da 550 mila euro che ci ha permesso di entrare nella fase operativa. Oggi gli scarponi usati vengono raccolti in circa 400 punti diversi in Europa, soprattutto nei negozi ma anche grazie ai contenitori predisposti nelle stazioni sciistiche del circuito Dolomiti Superski».
Possono essere consegnati solo i vostri marchi Tecnica e Nordica o il sistema è aperto a tutti?
«A tutti, e questa è una caratteristica fondamentale del progetto. Fin dall’inizio abbiamo pensato che il progetto dovesse essere condivisibile anche con i concorrenti, per avere un impatto davvero decisivo sulla filiera produttiva».
Finora avete raccolto e riciclato quasi 30 mila paia di scarponi. Dove avviene la fase di riciclo?
«Qui, nel nostro territorio, grazie ad accordi con una serie di partner. Gli scarponi raccolti vengono trasportati da Fercam con mezzi elettrici o alimentati a biogas. Viene fatta una prima selezione, perché alcuni possono essere ancora utilizzati e perciò vengono donati alla cooperativa sociale Insieme. Gli altri vengono triturati, separando i diversi materiali che hanno poi specifiche destinazioni. Noi li usiamo per tutta una serie di componenti di scarponi, sci e Moon Boot. I materiali delle scarpette interne vengono invece riutilizzati per la struttura dei materassi di protezione Liski che si trovano lungo le piste da sci».
Quanto riuscite a recuperare?
«Circa il 65% del peso degli scarponi. Ora abbiamo iniziato a inserire su ogni singolo scarpone prodotto un QR code ovvero un passaporto digitale che permette di identificare con precisione le caratteristiche dei materiali utilizzati. In questo modo potremo migliorare il processo di riciclo, ottenendo materiali con performance ancora migliori, in grado di essere utilizzati in parti dello scarpone che oggi vengono fatte interamente con plastica vergine. Anche grazie a questa innovazione, contiamo di arrivare a recuperare l’85-90% di ogni scarpone».
Anche i concorrenti adotteranno il QR code?
«Ci stiamo lavorando. Gli uffici della Commissione Europea ci hanno chiamato più volte per aggiornarsi sugli sviluppi e ora stiamo preparando un nuovo progetto per ottenere un ulteriore finanziamento, questa volta da 5 milioni di euro. La nostra idea è costituire un consorzio con altri soggetti interessati, con i quali condividere i risultati che abbiamo raggiunto e realizzare qui, sul nostro territorio, il primo impianto al mondo per il riciclo delle attrezzature sportive. Ci permetterebbe di effettuare le sperimentazioni necessarie a stretto contatto con la Ricerca & Sviluppo, aumentare la scala del processo, ridurre i costi fino a renderli del tutto comparabili con la plastica vergine. L’idea è poter passare da 30 mila a 300 mila paia riciclate. Abbiamo avviato i contatti con le istituzioni, perché potrebbe essere un progetto in grado di dare un ulteriore primato al distretto veneto dello Sportsystem».
Per associare altre aziende, i tempi non rischiano di allungarsi?
«Forse, ma noi siamo pronti e inizieremo comunque. A livello internazionale c’è molta attenzione: la World Federation of the Sporting Goods Industry, di cui sono il vicepresidente per l’Europa, ha ben presente che in termini di sostenibilità non si può andare molto oltre a quanto facciamo ora, se ci si limita a migliorare l’efficienza dei sistemi produttivi. Occorre un nuovo salto di qualità e il distretto dello Sportsystem può aprire una strada».
Tecnica produce circa un terzo dei tre milioni di paia di scarponi venduti nel mondo in un anno. Non temete di perdere un fattore di competitività, condividendo i risultati di Recycle your boots?
«Quello che conta per la nostra industria è creare un nuovo standard, prima che ci venga imposto dall’alto. E poi stiamo già lavorando su tutti gli altri articoli, gli sci, le scarpe per l’outdoor, i Rollerblade. Contiamo di poter essere sempre un passo avanti».
Riproduzione riservata © il Nord Est