Zignago, riciclare il vetro giova ai conti e all’ambiente
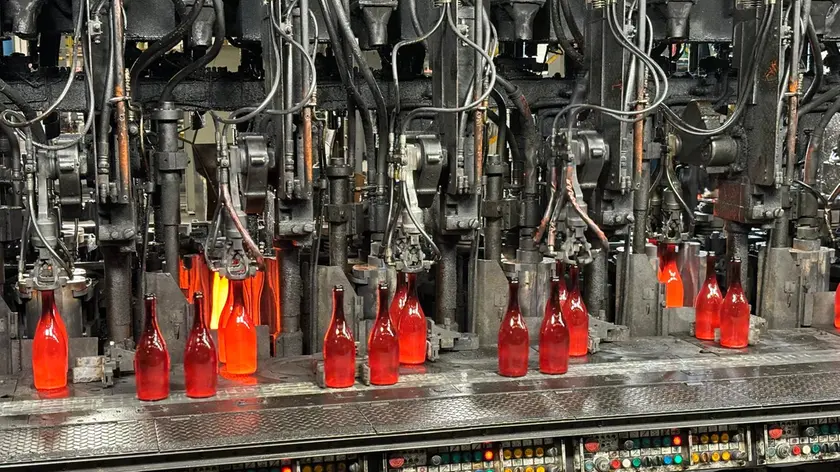
Un viaggio tra innovazione e sostenibilità alla scoperta di una filiera di riciclo completa, che parte dal trattamento del vetro inteso come rifiuto fino alla rifusione in vetreria. Il tutto sostenuto da energia prodotta in casa. Si tratta dell’ambizioso progetto realizzato nel corso degli anni, grazie alla sinergia delle aziende a cavallo tra Veneto e Friuli Venezia Giulia, dal Gruppo Zignago, colosso mondiale nella produzione di contenitori di vetro riciclato.
Ma qual è il percorso che compie un contenitore di vetro da quando viene scartato a quando assume nuova vita? Grazie all’appuntamento organizzato dal Consorzio per il recupero del vetro (Coreve) – collante tra i produttori e gli importatori di imballaggi di vetro di tutta Italia e attivo nella sensibilizzazione sulla raccolta differenziata – il Gruppo Zignago ha aperto le proprie porte offrendo la possibilità di conoscere più da vicino l’attività delle aziende del gruppo: dalla Julia Vitrum di San Vito al Tagliamento, polo di riferimento per il Nord Est per il riciclo, alla Zignago Vetro, storica vetreria di Fossalta di Portogruaro, passando per la Zignago Power, che si occupa della produzione di energia per alimentare l’intera vetreria e non solo.
La fase di riciclo
Il primo tassello che compone la filiera di riciclaggio del vetro è rappresentato, quindi, dalla Julia Vitrum, fondata nel 2019 con un investimento di 30 milioni di euro e un totale di 40 addetti. L’impianto è composto da due torri tecnologiche che all’interno racchiudono circa 300 macchinari, completamente automatizzati, deputati a separare il vetro dalle altre componenti che, a occhio nudo, non sarebbero visibili.
Un processo necessario considerando che il vetro viene considerato un materiale puro; per essere lavorato, quindi, non ammette la presenza di altri agenti. Scendendo nei dettagli delle varie fasi, dopo la prima selezione a occhio nudo, il vetro viene posizionato su dei nastri che lo portano all’interno delle due torri. Le macchine all’interno, sotto la supervisione degli operatori, svolgono analisi più approfondite separando ulteriormente il vetro dai materiali estranei non visibili a occhio nudo, che a loro volta vengono raccolti in depositi e spediti alle ditte di riciclo.
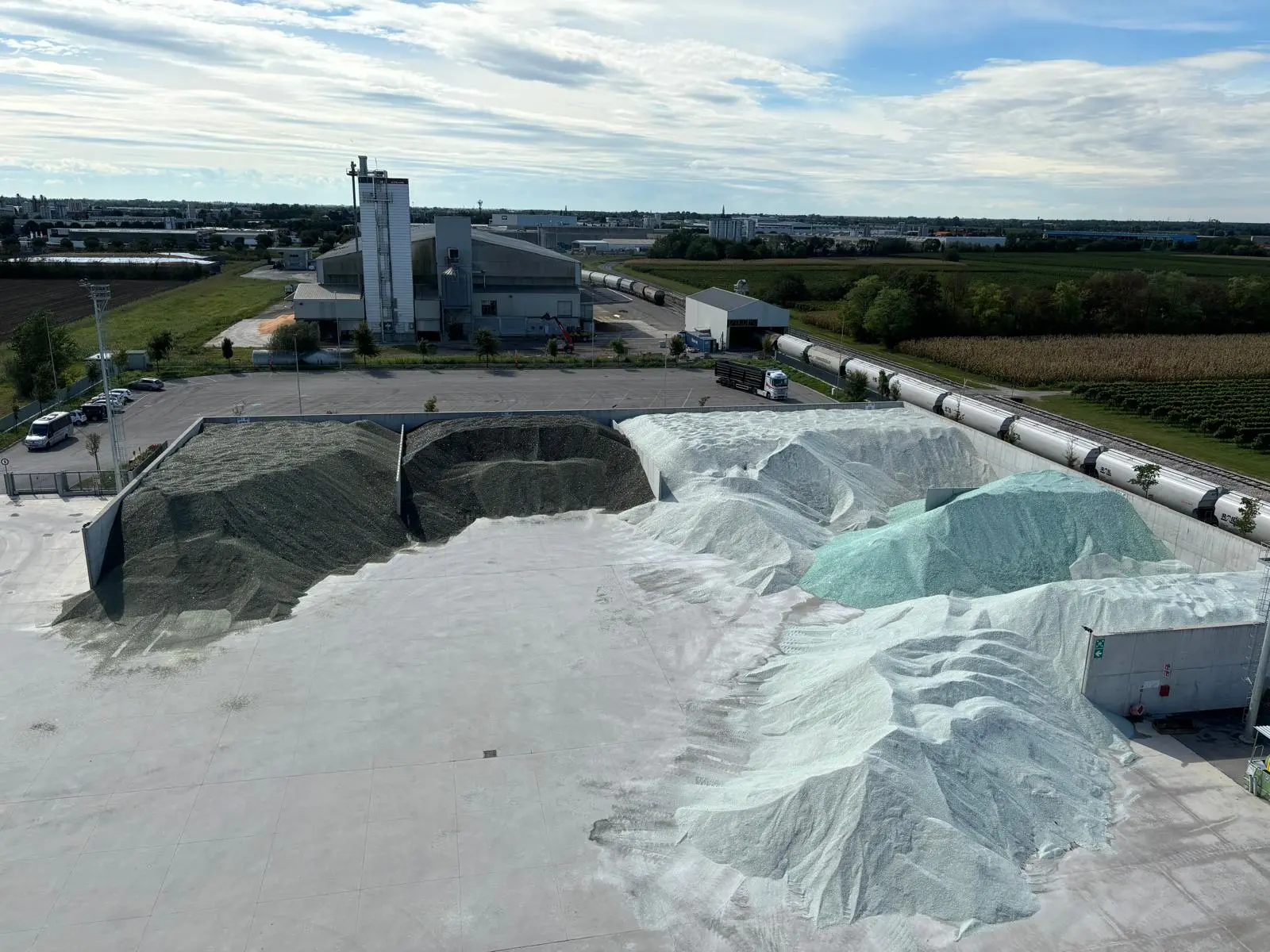
A quel punto daranno il via al processo per renderlo nuovamente pronto a essere lavorato. L’ultima fase riguarda la divisione delle varie tipologie di vetro, a seconda delle dimensioni e colore, e il loro invio in vetreria.
«Riciclare il vetro è fondamentale – ha spiegato il direttore dello stabilimento Dario Lorenzon –. Basti pensare che per realizzarne 1 chilogrammo sono necessari 1,2 chilogrammi di materie prime; ne consegue il consumo di montagne di sabbia per ricavare i minerali necessari, oltre all’inquinamento che si genera per il loro trasporto. Il riciclaggio permette anche di avere una riduzione del 30% circa sui costi energetici. La nostra realtà gestisce circa 300 mila tonnellate di vetro all’anno, 1.000 tonnellate al giorno, l’equivalenti dei rifiuti che produce annualmente una cittadina con 25 mila abitanti».
Dalla lavorazione al prodotto finito
Terminata la fase di riciclo ciò che si ottiene è un’enorme quantità di frammenti di pochi millimetri, che verranno inviati alle vetrerie, in questo caso alla Zignago Vetro. L’impianto, di 280 metri quadrati con 2.798 addetti si configura come un’area all’avanguardia dove ogni anno vengono prodotte circa 300 mila tonnellate di vetro. All’interno sono presenti tre forni, attivi tutto l’anno, ognuno dei quali lavoro tipologie di vetro diverse. Si tratta di strutture ad alta automazione, che fondono circa 320 tonnellate al giorno, attraverso l’uso di metano o elettrodi installati sul letto del forno.
Una volta che il vetro ha raggiunto la temperatura di 1.500 gradi vengono ricavate delle piccole gocce, inviate alle macchine stampatrici che si occuperanno di dare la forma necessaria. A seguire la fase del controllo qualità: i prodotti vengono analizzati da macchinari con una precisione assoluta, in grado di individuare anche minime imperfezioni.
Come ha sottolineato il direttore dello stabilimento Denis Bertusso, l’intero processo necessita di essere costantemente vigilato da figure esperte, in grado di intervenire qualora ce ne fosse bisogno. L’impianto, inoltre, è dotato di un circuito di raffreddamento ad hoc, che pesca l’acqua da un bacino interno.
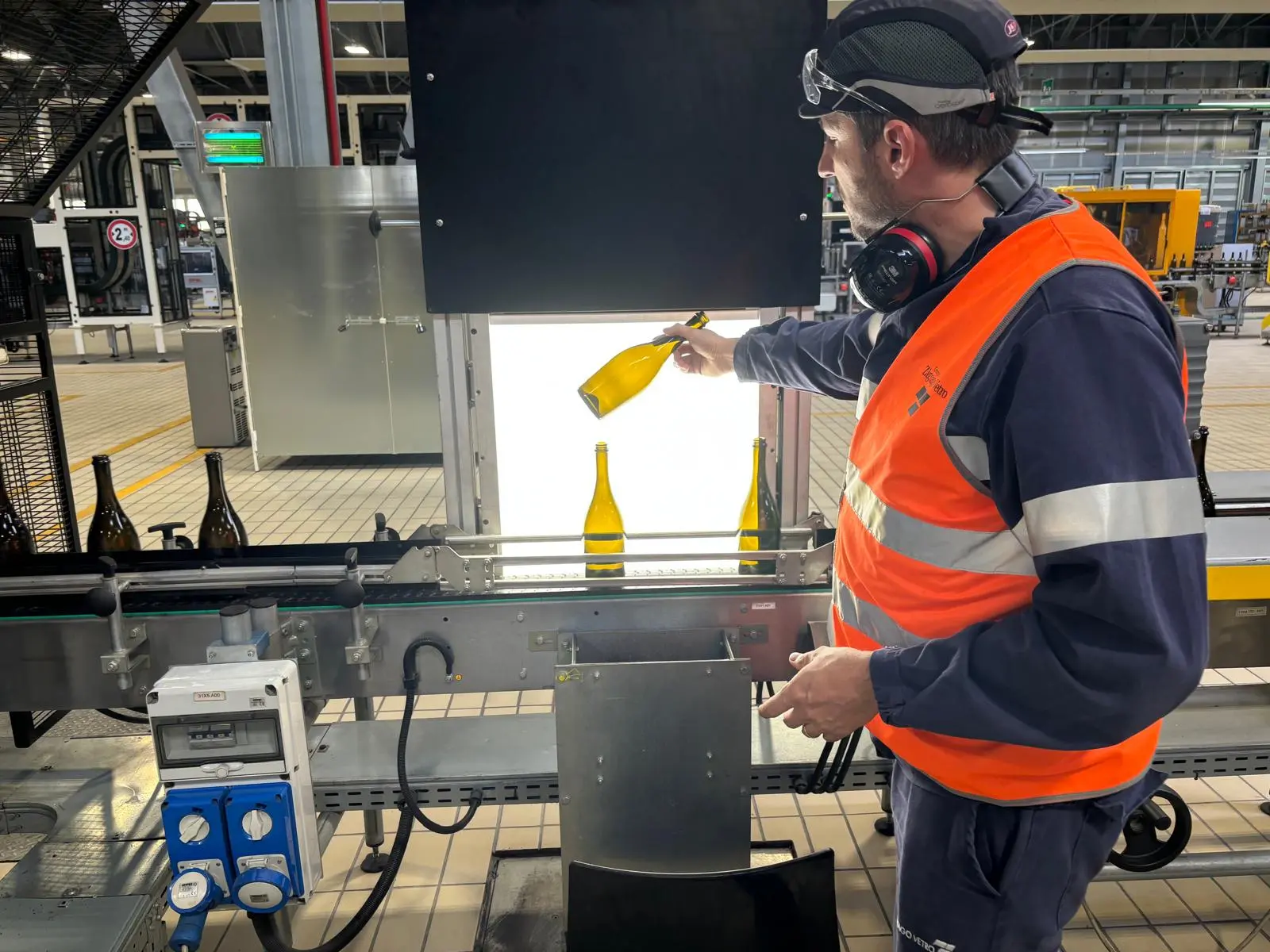
«Nulla va sprecato – ha precisato Bertusso –. L’acqua, infatti, una volta raffreddata ritorna nel bacino, creando così un ricircolo continuo. Nonostante il processo di lavorazione del vetro sia ad alta automazione, per noi le risorse umane ricoprono un ruolo fondamentale sulle quali vi sono investimenti costanti, in particolare sul fronte della sicurezza. Il nostro obiettivo, di anno in anno, è di azzerare gli infortuni; devo dire che stiamo percorrendo la strada giusta». Da sottolineare il fatto che, oltre ai contenitori venduti ai clienti, le bottiglie di vino realizzate in vetreria vengono utilizzate dalla cantina Santa Margherita, azienda del Gruppo Zignago, per imbottigliare il proprio prodotto.
Un percorso sostenibile
Zignago Vetro è fortemente impegnata nella sostenibilità, in particolare sull’efficienza energetica e la riduzione delle emissioni. La collaborazione strategica con Zignago Power, azienda del gruppo specializzata nella produzione di energia da fonti rinnovabili, è un esempio di questo impegno. Come ha spiegato l’amministratore delegato Andrea Bigai, si tratta di una sinergia indispensabile considerando che in un giorno la vetreria consuma la stessa energia che i pannelli fotovoltaici tradizionali producono in un anno.
La centrale viene alimentata dagli scarti derivati da produzioni agricole ma non solo, i quali non vengono trattati per ridurre le emissioni. Si tratta di un impianto da 50 megawatt termici, di cui 10 vengono riservati alla vetreria. Il consumo medio giornaliero per mantenere attiva la centrale si aggira intorno alle 500 tonnellate di materiali. Il calore prodotto, inoltre, non viene disperso ma contribuisce ad alimentare circa 200 utenze nelle vicinanze, tra cui anche la casa di riposo del comune di Fossalta. —
Riproduzione riservata © il Nord Est