Living Lab: le 12 imprese venete che fanno parlare di sé, nel libro di Gianni Potti
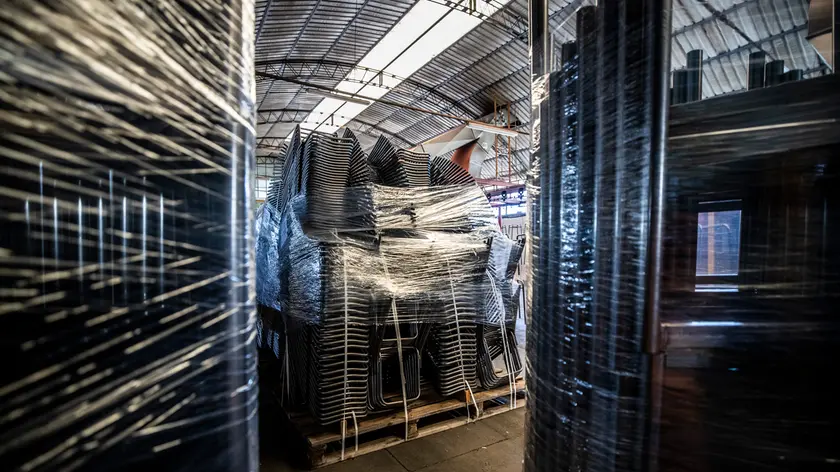
PADOVA. «Come dice sempre Alberto Bombassei, la quarta rivoluzione industriale, ovvero quella che chiamiamo Industria 4.0, ci accompagnerà almeno fino al 2030».
Inizia così “Industria 4.0, storie di macchine e di uomini” il nuovo libro di Gianni Potti, patron della più grande kermesse italiana di alfabetizzazione digitale che è Digitalmeet.
Una vera e propria anabasi, un viaggio, frutto di un percorso ormai decennale di approfondimento e reportage, nei concetti e negli strumenti ma pure nelle pratiche concrete e negli aneddoti di una quarta rivoluzione industriale in cui siamo pienamente immersi, dagli imprenditori ai professionisti fino a operai, commercianti, consumatori o esercenti.
Un testo che promette di diventare un classico della divulgazione in merito a un tema, quello della trasformazione digitale delle attività produttive, di quelle economiche ma anche sociali e individuali, che è il centro del nostro futuro di comunità.
Per presentare questo libro ma anche per affrontare le principali implicazioni concrete di un processo di innovazione profonda della nostra società, a partire dalle 18 prende il via, su Facebook, in diretta e disponibile a tutti, la prima tappa di un roadshow nazionale legato proprio ad “Industria 4.0, storie di macchine e di uomini”.
Ospiti della tavola rotonda inaugurale il ministro per lo Sviluppo Economico Stefano Patuanelli, il rettore dell’Università di Padova Rosario Rizzuto, il presidente di Carraro Group Enrico Carraro e l’autore Gianni Potti.
«Lo scopo del libro» spiega Potti «è quello di cercare di fornire ai protagonisti di questa quarta rivoluzione industriale gli strumenti e le nozioni strategiche per un’azione autenticamente innovativa nei propri ambiti di attività. Il libro contiene il racconto di esperienze concrete dell’applicazione dell’Industry 4.0 all’economia, ma contiene pure un breve dizionario con tutte le parole chiave della digitalizzazione.
«Un libro che abbiamo voluto molto aderente al presente non poteva non contenere considerazioni in merito agli effetti di breve e medio periodo del Covid e non poteva non concludersi con una visione del futuro in cui l’Industry 4. 0 dell’economia e l’evoluzione delle relazioni sociali tipica della società 5.0 si fonderanno in una nuova quotidianità evoluta».
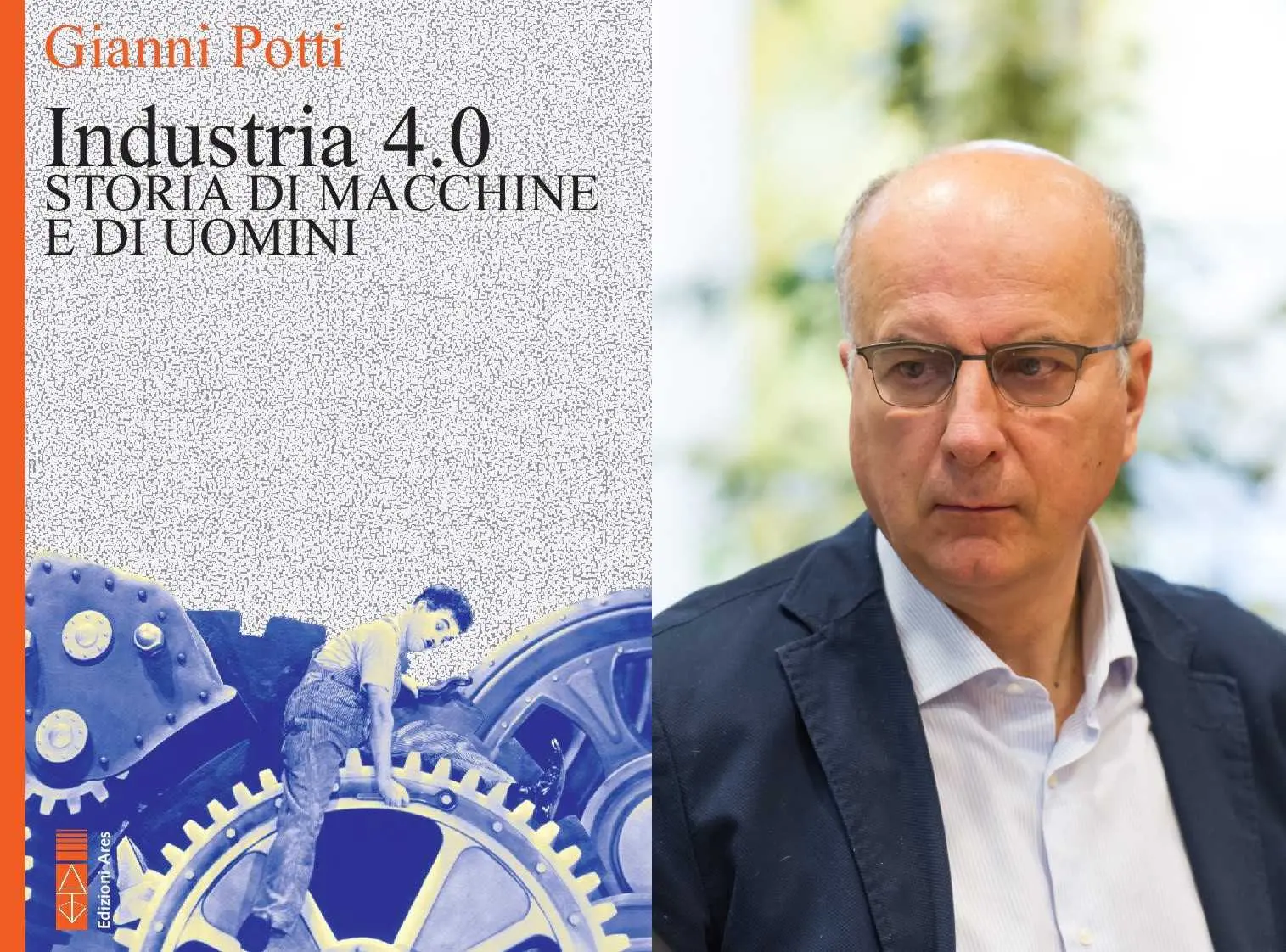
L'autore. Gianni Potti (Padova, 1959), imprenditore della comunicazione e del digitale, già vicepresidente dal 2011 al 2015 di Confindustria Padova, attualmente è Presi den te CNCT Confindustria Servizi Innovativi e tecnologici. Consigliere della Camera di Commercio di Padova. Advisor «Digital Innovation Hub» di Confindustria Ve ne to. Presidente di Fondazione Comunica. Cofoun der di Talent Garden Padova. Consigliere di Reteim presa. Partner di Digital Magics Triveneto. Membro del Comitato Scientifico Fondazione Saccone. Foun der di Digitalmeet. Nel dicembre 2017 ha ricevuto, come imprenditore innovativo, il prestigioso premio Volpato-Menato.
***
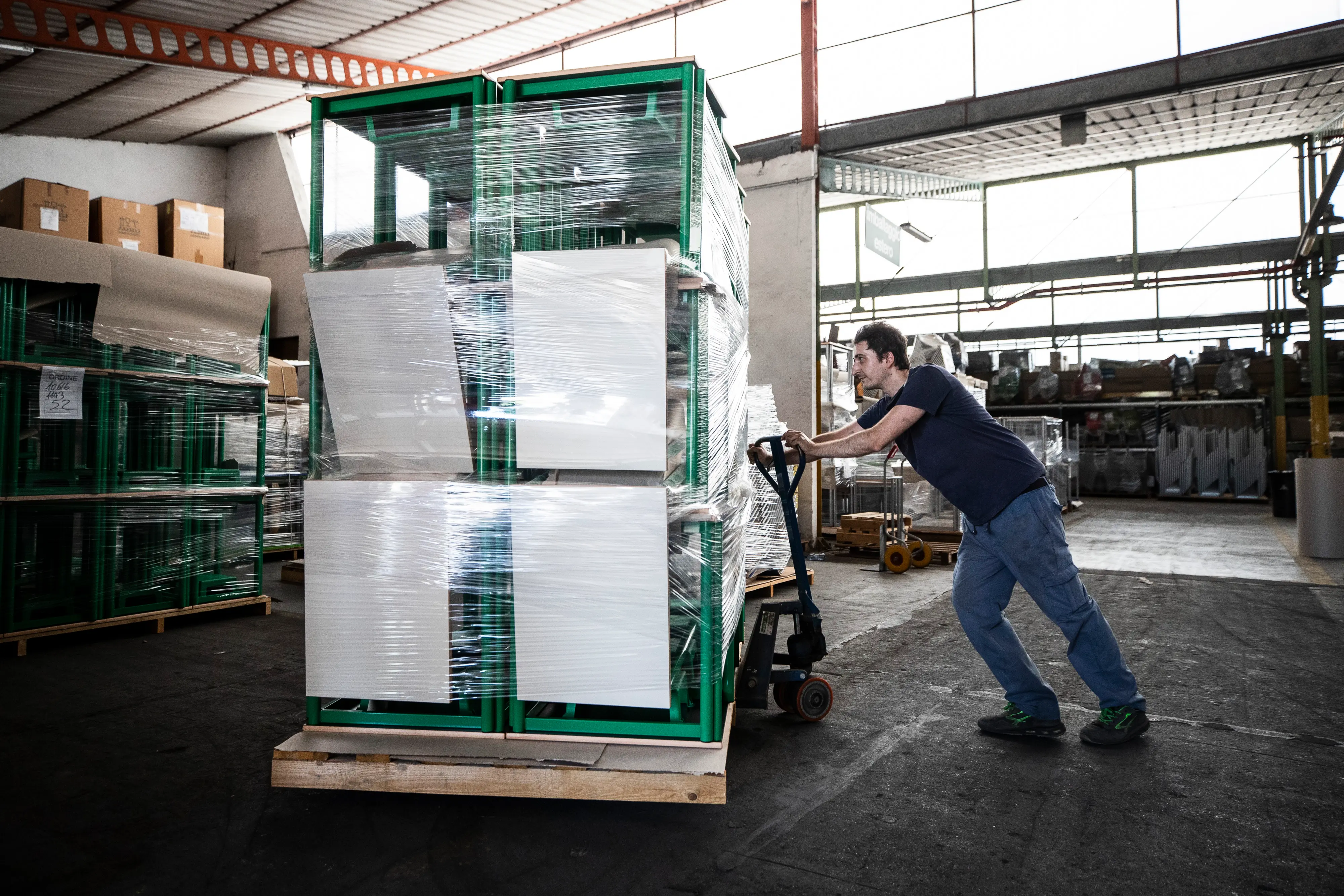
PILLOLE DI INDUSTRIA 4.0.
Living Lab: i 100 luoghi di industria 4.0 in Veneto. Sono luoghi in cui si possono toccare con mano applicazioni dell’Industria 4.0. Si tratta spesso di applicazioni sui processi che – essendo trasversali – possono essere mutuati da diversi settori, con un effetto moltiplicativo significativo. Un living lab che è anche un’esperienza mutuabile in altri territori
In Veneto Confindustria si è data, da tempo, un’agenda su Industria 4.0, costituendo un tavolo dedicato al tema del quale fanno parte tutte e sei le territoriali.
Nel corso degli ultimi dieci mesi il lavoro è partito dallo scenario generale, ha seguito le tematiche inerenti le misure di sostegno nazionali, la partita dei Digital Innovation Hub e Competence Center, approfondito il tema dei servizi in capo ai DIH e il modello di audit per le imprese. Insomma un’agenda fatta di tanti temi e tanto approfondimento, per arrivare ai due argomenti clou (almeno per ora), il documento per un “Progetto di Legge regionale 4.0″ e il progetto denominato “I 100 luoghi di Industria 4.0”
Il progetto.Confindustria Veneto da parte sua sta mettendo a punto un sito ad hoc con geolocalizzazione delle aziende per far raccontare le storie delle Industrie 4.0 anche con testi, foto e video, con approccio molto tecnico e utile per chi voglia comprendere come avviare un percorso 4.0
Fondazione Univeneto. Per selezionare i criteri di accesso e l’ammissione ad entrare nel progetto “I 100 luoghi di Industria 4.0” Confindustria si è rivolta alla Fondazione Univeneto, che raggruppa le quattro Università del territorio regionale ovvero quella di Padova, di Cà Foscari, dello IUAV e di Verona. Univeneto ha individuato un Comitato Tecnico Scientifico incaricato appunto di definire criteri scientifici e tecnologici di ammissione per le aziende e successivamente di valutare le candidature pervenute. I componenti individuati sono pertanto: Luciano Gamberini (UNIPD), Fabrizio Dughiero (UNIPD), Agostino Cortesi (Ca’ Foscari), Mario Pezzotti (UniVR), Francesco Musco (IUAV).
DOCICI CASI CONCRETI
Le imprese si aprono e si lasciano spiare e guardare. Tutto alla luce del sole. Tutto per dire al vicino: anche tu lo puoi fare, anche tu puoi essere maggiormente competitivo se introduci il 4.0 nei tuoi processi di produzione. Da qui in avanti vi troverete delle vere e proprie schede di imprese (una dozzina di vere e proprie PMI, di vari territori, settori merceologici e dimensionalità) scelte per i 100 luoghi con un cenno storico dell’impresa, il progetto 4.0 da toccare con mano, poi vantaggi e svantaggi di questo intervento, infine un po’ di sana vision su come l’imprenditore si immagina in concreto la propria impresa sempre più innovativa, oggi e nel futuro prossimo.
1 – GALDI
Più di 30 anni fa Galdino Candiotto, fondatore di Galdi e appassionato di meccanica, disegna e crea la prima riempitrice Galdi. La “Numero 1” nasce per rispondere ad un’esigenza della latteria di famiglia e di altre latterie locali: passare dal confezionamento nelle bottiglie di vetro ai cartoni in carta, un packaging più flessibile, economico e sostenibile.
PROGETTO
Il progetto MaSH (Machine System Health) ha reso i macchinari prodotti dall’azienda più innovativi, arricchendoli di tecnologie abilitanti quali ICT e meccatronica, per supportare la produzione delle aziende alimentari, i principali clienti GALDI, per evolversi e migliorare in termini di sicurezza alimentare, efficienza, qualità del prodotto finale. Infatti, l’industria alimentare ha esigenze di interconnessione e di interazione uomo-macchina molto spinte, ma allo stato dell’arte sono affrontate con soluzioni estemporanee, con l’implementazione di sistemi sviluppati ad hoc non trasferibili in altri contesti. I vari costruttori di macchinari, fino al momento dell’avvio del progetto, avevano delle singole soluzioni per affrontare le varie tematiche quali i servizi di manutenzione, assistenza da remoto etc, senza però un coordinamento tra di essi.
Vantaggi
Siamo soddisfatti del progetto, perché, oltre ad avere lanciato la prima versione in 12 mesi, siamo riusciti a formare un team con le competenze fondamentali per l'implementazione delle tecnologie caratteristiche dell'industria 4.0, mettendo le basi per un futuro avanzamento tecnologico dei prodotti e di conseguenza dell'azienda. Si è inoltre rafforzata l'immagine di GALDI come azienda innovativa, non solo verso i clienti, ma anche nel territorio, diventando attraente per i giovani talenti.
Svantaggi
Le risorse umane sono state la criticità maggiore in quanto nel corso di 12 mesi del progetto abbiamo dovuto sostituire tutte e tre le figure dedicate perché, anche grazie all’esperienza maturata con questo progetto, sono molto ricercate nel mercato. Altra criticità attualmente non ancora risolta è la diffidenza dei clienti a dare accesso alle macchine, sia per questioni legate alla sicurezza informatica, sia perché non sempre colgono i vantaggi offerti dal sistema.
VISIONE
Sono stati studiati nuovi servizi da offrire ai clienti per ampliare l'offerta, pre e post vendita. Il concetto base è quello di avvicinarsi a dei modelli di business più vicini alla "servitizzazione", ovvero essere più a contatto e vicini ai clienti, raccogliere direttamente i feedback dai macchinari per chiudere il loop della progettazione e, quindi, poter migliorare i prodotti. Creare maggiore consapevolezza delle performance dei prodotti (tramite dati sicuri), dà prove tangibili della qualità dei prodotti, quindi maggiore sicurezza all'area commerciale. Tutto ciò ci ha permesso di introdurre nuove tecnologie, ma soprattutto competenze da sfruttare per future innovazioni.
2 - TECHNOWRAPP
Abbiamo creato Technowrapp con un concetto semplice: se tutti entriamo al mattino convinti che questo sia il luogo dove meglio esprimersi, nel quale possiamo crescere, in cui le nostre capacità sono apprezzate, allora Technowrapp rispecchierà la parte migliore di noi e sia i nostri prodotti che il nostro servizio ne saranno la diretta espressione. Dal 2002 Technowrapp progetta e produce avvolgitori automatici per pallet e sistemi di movimentazione e trasporto pallet. Intralogika, la nuova divisione di Technowrapp, è specializzata nello studio e realizzazione di soluzioni per l’intralogistica, curando tutti gli aspetti della movimentazione e tracciabilità dei carichi all’interno delle aree produttive. Siamo un team di giovani esperti, ma curiamo ogni giorno il clima interno per ascoltare con voglia di imparare e garantire ai nostri clienti la miglior esperienza.
PROGETTO
Il nostro obbiettivo è quello di avere informazioni trasparenti in tempo reale, rivolte sia al nostro personale interno sia per i nostri clienti e clienti dei nostri clienti. Ci stiamo adoperando per implementare in azienda tutti i sistemi necessari per centralizzare tutte le informazioni dando dei KPI di controllo, attingendo da un unico contenitore denominato Data Lake. All'interno di quest’ultimo verranno trasferiti dati da ERP, CMR, PDM, MES, nonché, a breve, verranno interconnesse anche le macchine con sistemi di deep learning e machine learning. Verranno, inoltre, introdotti sistemi di monitoraggio tramite pistole barcode per agevolare la registrazione delle ore da parte degli operatori e monitorare in tempo reale l’efficienza e i costi sia di progettazione che di montaggio. Tramite il match di queste informazioni si potranno realizzare nuove strategie di vendita, analizzare andamenti di mercato, realizzare nuovi prodotti mirati per certi settori, dando ampio spazio al sistema di analisi mediante un software denominato CORPORATE PERFORMANCE MANAGEMENT (CPM). Questo progetto così articolato è stato inoltre condiviso con tutta l'azienda, organizzando una serata a tema, presentando un concorso a premi, con l'obbiettivo di stimolare la creatività e la partecipazione di tutti i dipendenti
Vantaggi
Efficientare a 360° tutte le funzioni aziendali con l'obbiettivo di ottimizzare i costi ed aumentare la qualità del lavoro. I principali motivi di soddisfazione sono il riscontro dei colleghi e la sempre più tempestività delle risposte, essenziale per un'azienda dinamica come la nostra.
Svantaggi
Le principali difficoltà sono state e sono quelle della mentalità delle persone e la preparazione della base dati per poi selezionare lo strumento software adeguato.
VISIONE
L’efficientamento di tutti i reparti andando a produrre meglio e a minor costo. Disponibilità di KPI di controllo precisi e in real time per monitorare l'andamento aziendale a vari livelli.
3 - SARIV
Sariv è un’azienda produttrice di rivetti a strappo, princi-palmente per il settore automotive che, oltre alla sede pro-duttiva principale italiana (provincia di Padova) dispone di 5 filiali distributive in Europa: Croazia, Polonia, Repubblica Ceca, Slovacchia e Russia. Il mercato di riferimento è prin-cipalmente estero (85%), servendo i maggiori distributori del mercato europeo ed extra-europeo. Nel 2008, il tipo di mercato principale per l’azienda era di ferramenta e applicazioni ‘standard’. In seguito ad un processo di forte rinnovamento interno, necessario per superare le difficoltà portate dalla crisi economica, Sariv si è prefissata l’obiettivo di diventare un Competence Center di riferimento per il settore dei rivetti, valorizzando il pro-dotto attraverso i servizi ad esso collegati, dalla progetta-zione, alla produzione e alla fornitura di dati sul prodotto stesso.L’azienda oggi ha un fatturato, in crescita, di circa 7,5 milioni di euro annui e può contare su 40 dipendenti (di cui 25 blue collar). Le logiche di produzione adottate sono principal-mente MTS e MTO.
PROGETTO
Una trasformazione legata implicitamente al cambio di modello di business necessario per uscire dalla crisi del 2008/2009, con una digitalizzazione progressiva dei processi produttivi per ottenere dati, per arrivare alla rintracciabilità totale dei prodotti su piattaforma digitale. Step successivi sono stati legati alla gestione digitale, sulla stessa piattaforma, dei controlli qualità, fino ad arrivare paperless e quindi con una gestione totale su base digitale delle informazioni del processo produttivo e delle funzioni collegate. Oltre il 70% degli investimenti per la digitalizzazione iniziale avvenuti pre-Calenda, con svantaggi dal punto di vista economico, ma vantaggi competitivi rispetto ai nostri concorrenti.
Vantaggi
SARIV ha fatto passi da gigante in termini di possibilità di controllo e di sviluppo dei progetti, e la crescita stessa dell'azienda (fatturato, EBITDA) non sarebbe stata possibile senza tale passaggio digitale. Essere diventati casi di studio per varie Università, per organizzazioni sindacali sulla trasformazione del lavoro, ed in particolare la connessione che grazie a questo abbiamo creato con il Politecnico di Milano è stata una grande soddisfazione. La digitalizzazione ha dato la possibilità all'azienda di poter avere accesso ad applicazioni impossibili da raggiungere senza la trasformazione avvenuta. Il mercato principale è divenuto l'automotive, dove il risk management è spinto, e la possibilità di ottenere dati in tempo reale per controlli real-time degli andamenti dei processi, e di gestione degli scostamenti, ha fatto la differenza. Per un'azienda piccola come noi, con un prodotto povero, non sarebbe pensabile avere 'controllo' sui prodotti montati su una moltitudine di automobili se non avessimo intrapreso un percorso del genere.
Svantaggi
Punti di difficoltà più che punti deboli sono stati in fase iniziale l'introduzione per la forza lavoro strumenti digitali a loro prima sconosciuti. Ma obiettivamente l'essere partiti così in anticipo ha fatto sì che il nostro processo sia stato più graduale e meno traumatico rispetto ad altre realtà.
VISIONE
Praticamente quasi tutti adesso viene discusso in ottica digitalizzazione. Gli investimenti maggiori degli ultimi anni (da nuove figure introdotte in azienda, ad investimenti in piattaforme informatiche, al risk management dei dati) sono tutti legati al 4.0.
4 - IMESA
Imesa S.p.A è un’azienda del settore metalmeccanico che si occupa della produzione di macchinari per il settore lavanderia. La progettazione e la produzione sono realizzate tutte interamente all’interno dello stabilimento aziendale.
Nella filosofia del miglioramento continuo che ci contraddistingue, abbiamo avviato, a partire da settembre 2018, un processo di lean transformation - che si concluderà nel 2021 - che prevede un passaggio ad una gestione aziendale più snella e centrata sul cliente.
Si è concluso un primo processo di trasformazione di una linea produttiva e sono in corso i progetti di trasformazione del flusso progettuale e del flusso commerciale, nonché l’implementazione di alcuni cantieri SMED per ottimizzare il set up dei macchinari.
È stato, infine, avviato un progetto di formazione offerta a tutti i collaboratori sulle principali tematiche del lean thinking.
PROGETTO
Stiamo realizzando un progetto di collegamento IoT con tutte le macchine di nostra produzione (lavatrici, essiccatoi e mangani per lavanderia industriale). L'obbiettivo che ci siamo dati è avere un controllo telemetrico sulle macchine, la possibilità di fare della diagnostica predittiva, avere una diagnosi continuativa sui consumi di detergenti, modificare i programmi di lavaggio a distanza su richiesta del cliente, inviare aggiornamenti software e firmware, infine poter noleggiare le nostre macchine direttamente ai clienti finali con la formula del "pay per use".
Oltre ai nuovi prodotti non va trascurato che stiamo investendo anche nella produzione con l’acquisto di nuovi macchinari e lo sviluppo di nuove tecnologie e nella gestione (computer e risorse umane).
VISIONE
Riteniamo di poter avere vantaggi tangibili quando il progetto avrà raggiunto la piena operatività. Da un punto di vista strategico l’utilizzo di questa nuova tecnologia ci consentirà di:
- Disporre di un maggior numero di dati;
- Disporre di maggiori informazioni e capacità di predizione dei rischi di guasto;
- Disporre di informazioni dirette e precise, generate direttamente dalla macchina, sui guasti;
- Aumentare il nostro fatturato grazie ad una innovativa formula di vendita.
L'IOT ci sta aprendo un mondo nuovo sconosciuto che sicuramente cambierà il nostro approccio al mercato e che ci consentirà, in futuro, di avvicinarci alla gestione dei Big Data.
5 - ITALCAB
Italcab S.p.a. dal 1980 progetta e costruisce cabine per macchine industriali, quali escavatori, pale gommate, rulli compressori, gru, battipista.
La sua attività parte dalla progettazione, sviluppo del prodotto, prototipazione e preserie, per arrivare alla produzione di serie della cabina.
Le cabine sono realizzate in acciaio, verniciate in cataforesi e assemblate con porte, cristalli, rivestimenti, impianti idraulici, elettrici, termo-condizionatori, ecc.
Oggi, Italcab produce più di 12.000 cabine all’anno, con un fatturato complessivo superiore a 47 milioni di euro (dati 2018), di cui il 75% verso l’estero.
I lavoratori sono circa 200, impiegati in attività di ufficio (ca. 45 persone) e nei reparti carpenteria (ca. 30 persone), saldatura (ca. 55 persone) e assemblaggio (ca. 60 persone).
PROGETTO
Dopo la crisi del 2008-2009, nella quale il fatturato di Italcab è sceso del 70%, l’azienda ha reagito alle trasformazioni del mercato e ha, nel corso degli anni, modificato la propria organizzazione, per riuscire a gestire prodotti e processi più complessi e adeguare il proprio processo produttivo alle variazioni della domanda.
L’azienda ha già nel 2006 avviato l’informatizzazione dei reparti produttivi, nel 2008 ha ultimato la gestione a barcode del magazzino di componenti d’acquisto, nel 2011 l’informatizzazione del reparto di assemblaggio, nel 2016 del reparto di carpenteria e, nel biennio 2018-2019, sta portando a termine l’informatizzazione del reparto di saldatura e del magazzino di materie prime in acciaio.
A partire dal 2016, l’azienda ha avviato un programma di investimenti in beni strumentali, con l’obiettivo di modernizzare e automatizzare i reparti interni. Il volume di investimenti nel periodo 2016-2019 in beni strumentali è stato pari, in media, al 2,4% del fatturato e ha coinvolto tutti i reparti produttivi.
Nello stesso periodo, è aumentato il personale impiegatizio, con gli obiettivi di migliorare il servizio al cliente e la qualità del prodotto e di controllare e ridurre i costi esterni.
Questa trasformazione ha cambiato anche il posizionamento di Italcab sul mercato europeo delle cabine per macchine industriali: in un mercato che non ha recuperato i livelli precedenti alla crisi (nel 2017 il numero di macchine prodotte in Europa è stato inferiore del 30% rispetto al 2007), Italcab è riuscita a migliorare il proprio posizionamento, migliorando la qualità del prodotto e del servizio offerto ai clienti e proponendosi come fornitore capace di gestire prodotti complessi, anche in presenza di volumi di vendita contenuti.
Questo posizionamento, oltre a consentire un recupero e un miglioramento dei livelli di vendite e di redditività precedenti alla crisi, offre maggiori garanzie nel caso di una crisi di settore, stante il maggior numero di modelli e di clienti presenti nel portafoglio aziendale.
Nel 2018, l’azienda ha introdotto nel proprio sistema produttivo un sistema informatizzato MES (Manufacturing Execution System), sviluppato dalla società Sogea S.r.l., che, affiancando i sistemi ERP e MRP già presenti, migliora la gestione delle fasi produttive interne e esterne e consente il collegamento diretto ai macchinari produttivi.
Attraverso il MES l’azienda potrà importare dall’ERP gli ordini di lavorazione, caricare da remoto i programmi nelle macchine, assistere gli operatori con istruzioni, monitorare i parametri macchina registrando avanzamenti e anomalie, eseguire gli avanzamenti di produzione e lo scarico dei materiali nell’ERP, tracciare i materiali utilizzati. Si realizza in questo modo un’integrazione tra i macchinari e il sistema logistico della fabbrica.
Vantaggi
- Uno stretto collegamento tra le richieste dei clienti e i reparti produttivi;
- Un’analisi automatizzata e continua di capacità e fabbisogni produttivi;
- La tracciabilità in tempo reale di lavorazioni, materiali, tempi, stato macchina;
- La dematerializzazione delle informazioni raccolte;
- L’automazione di attività a basso valore aggiunto;
- La nascita e lo sviluppo di competenze nuove e trasversali.
Criticità
- Dimensionare e sostenere il volume di investimenti richiesto dalla trasformazione del sistema produttivo;
- Individuare i partner che hanno la volontà e la capacità di condividere il percorso
VISIONE
Italcab ritiene che la digitalizzazione dei processi aziendali sia una delle caratteristiche che maggiormente la differenzia dai propri concorrenti. Unita a un’organizzazione fondata sui processi e sulla trasversalità tra le funzioni aziendali, la digitalizzazione consente di aumentare il livello di servizio offerto ai clienti, la qualità e la produttività interna.
Inoltre, prepara l’azienda e le persone che la compongono alle sfide del futuro, sviluppando nuove competenze e relazioni, verso l’interno e verso l’esterno.
6 - GASPARINI
Gasparini S.p.A. è una azienda di riferimento per la progettazione e produzione di macchinari hi-tech per l'industria della lavorazione dei metalli, specializzata in linee di profilatura per lamiera con spessori da 0,2 fino a 12 mm.
Progetta e realizza impianti su commessa, macchine automatiche o semiautomatiche per la deformazione a freddo dei metalli (acciaio, rame, alluminio, Zinco –Titanio, Inox, acciaio alto resistenziali, ecc.).
Gli impianti integrano, a seconda delle esigenze produttive, sistemi di punzonatura, foratura, piegatura, saldatura, taglio, movimentazione e imballaggio, che vengono anche essi progettati e realizzati internamente.
Le linee producono profili in metallo che costituiscono prodotti finiti o parti semilavorate, destinate all'utilizzo in diversi settori industriali, quali: Costruzioni, Logistica, Energia e Automotive.
Gli impianti Gasparini sono utilizzati in tutto il mondo da più di 1.500 aziende.
PROGETTO
Il progetto in corso prevede l’implementazione di una nuova piattaforma per la gestione di tutti i processi aziendali attraverso sistemi integrati che comunichino tra di loro, sostituendo quelli esistenti e implementando nuovi software, anche con l'utilizzo di un nuovo sistema ERP per la gestione dell’interno ciclo di vita delle commesse.
La creazione offerte avviene con un programma di simulazione impianto e relativa preventivazione, mentre la gestione acquisti e logistica è gestita attraverso un portale web dedicato a offerte e ordini dei fornitori con abbinamento e consegna in automatico delle specifiche a disegno.
La pianificazione della produzione è resa dinamica grazie un software specifico e alla raccolta dati di fabbrica con MES (raccolta dati, controllo e avanzamento delle fasi di produzione, gestione delle risorse di produzione, tracciabilità del prodotto e stato della macchina, monitoraggio dei componenti in produzione). Inoltre, ogni operatore addetto alla produzione è dotato di tablet e smartphone per la registrazione MES e consultazione PDM.
Altre peculiarità del progetto 4.0 che l'azienda ha in atto sono:
- controllo di gestione dinamico con analisi per commessa e WIP;
- sistema documentale integrato (DMS) per tutta la documentazione relativa alle commesse;
- archiviazione documentazione tecnica, creazione automatica o a chiamata di file di scambio (pdf, dxf, step);
- ottimizzazione e controllo dei processi di vendita.
Il progetto comprende, inoltre, la dotazione di nuove attrezzature integrate nel processo produttivo, per aumentare il gradiente di efficienza e di registrazione dei dati di processo. Sono sati inseriti: un magazzino automatico per la gestione della componentistica standard collegato a ERP per lista prelievi automatica, un distributore automatico per distribuzione utensili, strumenti di misura e DPI, un centro di lavoro verticale connesso al MES e una macchina prova materiali per controllo snervamento e carico di rottura.
Vantaggi
Il progetto sta contribuendo a migliorare le performance aziendali, grazie ad importanti punti di miglioramento, quali: l’univocità e congruenza dei dati, lo snellimento della costruzione delle specifiche tecniche al fine di ottimizzare i flussi della Supply Chain, il monitoraggio degli eventi critici di commessa, la riduzione degli strumenti esterni al sistema, il controllo degli avanzamenti presso i fornitori esterni e l’utilizzo del controllo di gestione integrato.
Svantaggi
L'operazione richiede un tempo di sviluppo importante, dovendo coinvolgere fasi operative che non possono essere interrotte. Richiede una grande disponibilità da parte di tutti gli attori coinvolti in termini di tempo e determinazione.
VISIONE
Il processo di miglioramento innescato comporta la possibilità di avere una maggiore certezza delle informazioni aziendali e un monitoraggio più puntuale, consentendo di valutare le strategie aziendali da seguire. Tutti aspetti prioritari lavorando su commessa con tempistiche realizzative medio lunghe.
7 - BAXI
Baxi S.p.A. è un'azienda italiana produttrice di apparecchi per il riscaldamento facente parte della multinazionale olandese BDR Thermea. La filosofia Baxi è da sempre al servizio di soluzioni tecnologicamente avanzate di semplice utilizzo.
PROGETTO
Il principale progetto di innovazione digitale realizzato ad oggi in azienda riguarda la messa in funzione della nuova linea di produzione caldaie murali a condensazione di nuova generazione. Questo impianto, internamente chiamato "linea NG1", è nato per la realizzazione di una nuova gamma prodotto e con l'obiettivo di seguire la domanda del mercato con una maggiore flessibilità, elevare il livello di qualità offerto al cliente e migliorare i processi produttivi e logistici interni attraverso l'applicazione dei principi Lean parte delle politiche Operations aziendali già da diversi anni. La linea può produrre da 35 a 450 caldaie murali per turno, attraverso l'utilizzo di 12 diversi ritmi produttivi a seconda della domanda del cliente. Sono utilizzati sistemi di tracciabilità dei componenti, del processo e degli operatori di assemblaggio, sistemi "pick to light" a supporto dell'attività e della qualità, controlli visivi automatici con fotocamere, sistemi di registrazione dei parametri e degli esiti dei test via cavo o wifi ed istruzioni di lavoro digitali caricate per ogni singolo prodotto ed in tempo reale. Il tutto, attraverso l'utilizzo di un tag RFID e di antenne di lettura automatica posizionate lungo tutto il processo di assemblaggio. Sono stati inoltre inseriti alcuni sistemi di movimentazione automatica, quali robot, manipolatori ed etichettatrici automatiche, per eseguire quelle attività che potrebbero gravare maggiormente sull'operatore in termini di ergonomia.
Vantaggi
Il grado di soddisfazione dopo l'implementazione del progetto è piuttosto elevato. Il livello di qualità complessiva generato dall'impianto è superiore a quello medio rilevato nelle altre linee produttive, questo grazie anche alle nuove tecnologie introdotte a supporto dell'operatività. Il "cambiamento di approccio", dopo la fase iniziale di start-up dell'impianto, è stato accolto in maniera positiva dal personale impegnato. La raccolta puntuale dei dati di tracciabilità di componenti e processo ci permette di arrivare ad un livello di analisi dei processi difficilmente raggiungibile senza l'utilizzo di tecnologie abilitanti. L'ampia pianificabilità dell'output permette un migliore controllo dei livelli di stock del prodotto finito e le tecnologie in gioco permettono inoltre di produrre lotto minimo pari ad un singolo pezzo laddove fosse necessario, senza perdere produttività. Chiaramente tutto questo ha richiesto importanti attività di progettazione, preparazione e test iniziali.
VISIONE
Nel concreto quanto detto sopra ha portato ad un consistente aumento della flessibilità in produzione per l'area interessata. Aumento in senso generale del know-how aziendale, per il personale coinvolto nella progettazione e implementazione ma anche per il personale operativo di produzione, che lavora con strumenti di complessità diversa dal passato ma senza particolari difficoltà. Minore utilizzo complessivo di manodopera e ridotti rischi dal punto di vista ergonomico. Controllo del processo e del prodotto di livello decisamente superiore e possibilità di rintracciare in futuro eventuali problemi nati per difettosità di particolari lotti o seriali di componenti.
L'utilizzo ed una maggiore conoscenza acquisita riguardo le nuove tecnologie implementate, ha fatto e sta facendo sì che in tutti i nuovi progetti o nella revisione di processi esistenti, vi sia una maggiore propensione all'utilizzo di quanto offerto da un approccio "Industry 4.0". I vantaggi, nel tempo, risultano evidenti. In modo particolare l'azienda si sta impegnando ad estendere la raccolta dei dati di tracciabilità a tutti i processi produttivi laddove possibile, utile e vantaggioso. Un altro percorso intrapreso è quello rivolto alla digitalizzazione delle istruzioni di lavoro. Si passa poi agli aspetti legati al mondo della logistica dove, anche in questo caso l'approccio è sempre più paper-less. Inoltre lo sviluppo ed immissione nel mercato di sistemi e prodotti che permettono il remote monitoring o il controllo remoto sono sempre più attuali.
8 - COMUNIAN
La nostra azienda, nata nel 1973 opera nel settore del commercio all’ingrosso di Vini, birre e bevande nelle provincie di Padova, Vicenza, Rovigo e Venezia. Il settore di riferimento è quello dell’Horeca.
Ad oggi abbiamo circa 30 dipendenti tra agenti, magazzinieri, consegnatari e impiegati. Acquistiamo direttamente dai principali produttori, in alcuni casi importiamo, dopo un’attenta analisi della qualità dei vini, da aziende selezionate estere, come nel caso di maison francesi o distillerie scozzesi, e distribuiamo i circa 2.000 articoli trattati a ristoranti bar, caffetterie e Pub con servizio di consegne capillari e frequenti ai nostri clienti. Il settore estero viene coperto solo in alcuni casi grazie a qualche cliente che ordina con frequenza trimestrale circa. Abbiamo un marchio di vini di proprietà, il Prosecco Cà del Sole che ci dà molta soddisfazione.
Abbiamo circa 20 camioncini che quotidianamente percorrono le strade delle 4 provincie coperte.
La nostra sede situata a Padova in Via Svezia 5 in zona industriale, si trova in una zona baricentrica rispetto ai clienti e comoda a tutte le principali vie. Qui abbiamo un magazzino di 3 .000 mq circa dove abbiamo utilizzato alcune tecnologie interessanti per migliorare le condizioni lavorative di tutti gli operatori.
PROGETTO
Il progetto nasce dalla volontà di alleggerire il lavoro dei magazzinieri. In pratica abbiamo sostituito il software di magazzino con uno più performante. Abbiamo interfacciato questo software con un magazzino automatico per la gestione di vassoi ( gestisce 100 vassoi da 3,4 mt x 0,80 con portata totale di 30.000 bottiglie), due monitor da 55 pollici, una rulliera fasciapallet con riconoscimento del pallet , pesatura ed etichettatura automatica, un trenino porta pallet per il picking che gestisce fino a 12 ordini per viaggio e un muletto frontale per gli spostamenti dei pallet interi.
Gli ordini presenti nel gestionale aziendale, dopo un controllo “contabile” vengono accorpati per consegnatario e spediti poi al software di magazzino. Qui la merce viene divisa per:
1) Pallet interi da abbassare prima di procedere con i prelievi, in modo che gli altri preparatori non debbano abbassare i pallet posizionati alti.
2) Pallet interi da prendere direttamente dalla scaffalatura e mettere in postazione di uscita, nel caso che nell’ordine ci siano pallet interi. Queste due prime informazioni vengono gestite dal carrello frontale dotato di terminalino Wifi e pistola laser
3) Merce da preparare con commissionatore su un singolo pallet, nel caso di ordini piccoli che vengono accorpati su un unico pallet per ogni consegnatario, non abbiamo limiti di numero massimo di ordini inseribili in un pallet. Qui vengono usate delle pistole wifi (radiofrequenza).
4) Treni: questo è il sistema più utilizzato e più performante per la preparazione della merce. Attraverso questi treni, viene preparata circa l’80 % della merce ogni giorno.
In pratica i treni si preparano da terminale in ufficio. Si compongono i pallet contenuti nei vagoni in base agli ordini, considerando una portata massima di 500/550 Kg a pallet: si fa in modo di raggiungere questo peso o comunque avvicinarsi il più possibile in modo che ogni treno possa preparare circa 2.000 kg per ogni giro, avendo 4 pallet ogni treno. Una volta accorpati questi ordini all’interno del treno, il magazziniere gestisce la preparazione tramite il terminale wifi presente sul trattore, che lo informa sul tipo di articolo che deve prelevare, sulla sua ubicazione e sul totale del prelievo da effettuare nonché su quale pallet e relativa quantità da mettere. In ogni vagone ci sono altri monitor che segnalano la quantità per pallet e delle luci a led si illuminano per segnalare meglio quale è l’esatto pallet. Questo per ogni articolo da prelevare. Verso la fine del percorso ci si avvicina al magazzino automatico che si muove in autonomia a seconda dell’articolo da prelevare e posiziona il relativo o i relativi “n” vassoi al piano terra, in modo da permettere il prelievo all’operatore, anche qui con un led che segnala dove si trova esattamente l’articolo da prelevare. Alla fine di tutti i prelievi il treno si posiziona perpendicolarmente su una rulliera lunga circa 20 metri. Questa rulliera, riconosce il treno e si mette in movimento ogni volta che viene “sganciato” un pallet dal treno. Qui il pallet viene riconosciuto tramite un lettore laser, viene controllato il peso e poi viene fasciato ed etichettato col numero di baia di uscita, nome dell’autista che deve caricare il pallet e nome dei clienti presenti all’interno. A questo punto quando arriva l’autista si trova la file di pallet da caricare e la merce parte.
Tutto questo lavoro viene monitorato in tempo reale tramite due monitor, di cui uno in ufficio e uno in magazzino, che permettono di far capire a chiunque, tramite un “contapeso” simile ad un contachilometri, a che punto di una scala che va da 0 a 100 siamo posizionati. Questo “contapeso” ci ha permesso di “quantificare” il lavoro giornaliero e di regolare la forza lavoro presente in magazzino. I magazzinieri riescono a spostarsi nelle varie lavorazioni in base al fabbisogno esatto e a suddividersi meglio i ruoli all’interno del magazzino.
Vantaggio
Questo sistema ci permette di essere molto più veloci nella preparazione della merce, evitando moltissimi errori. Ci ha evitato i numerosissimi giri che prima venivano effettuati anche a vuoto, tutto sommato abbiamo anche un buon risparmio energetico in quanto i treni fanno solo percorsi ad anello mentre prima era tutto un zigzagare con percorsi almeno 5 volte superiori, tutto è più fluido e comprensibile da tutti. Anche a livello emotivo c’è più tranquillità e maggior precisione.
Inoltre la rulliera che verifica il peso, fascia il pallet ed etichetta, ci evita di fasciare a mano il pallet, operazione molto fastidiosa soprattutto a livello di equilibrio dell’operatore.
Svantaggio
L’unico svantaggio, se si vuole trovarlo per forza, è il prezzo pagato, ma che è stato comunque pienamente ripagato dagli straordinari evitati.
VISIONE
Forte di questa esperienza molto interessante del magazzino, stiamo portando a termine un’ulteriore tecnologia sempre all’interno del nostro settore. Quello del telecontrollo da remoto dei parametri degli impianti di spillaggio.
Siamo già in fase di test con un prototipo che ci permette di raccogliere i dati di funzionamento ed intervenire sui parametri fondamentali degli impianti, sia in maniera automatica programmata sia in maniera manuale, e di visionare le varie problematiche che spesso sorgono, evitandoci inutili trasferte dei tecnici. È una cosa ancora non presente nel mercato ma che stiamo creando appositamente.
Altre idee ci sono, ma ancora non sono state portate avanti, come ad esempio un sistema di autocarri elettrici, ricaricati da batterie estraibili che potrebbero essere ricaricate in magazzino tramite pannelli fotovoltaici e sostituite al momento del carico scarico col muletto, oppure un sistema per lo scarico del materiale dai camion tramite dei manipolatori elettrici che evitano sforzi agli autisti/consegnatari, ma ancora non abbiamo trovato partner validi.
Siamo fortemente fiduciosi nelle tecnologie 4.0. C’è solo da avere nuove idee e fantasie.
9 - PRESSOFUSIONE SACCENSE
Pressofusione Saccense è un’azienda metalmeccanica di medie dimensioni che si occupa della produzione e lavorazione di getti pressofusi in alluminio.
L’azienda nasce nel 1981 come fonderia di pressofusione e nel corso degli anni, effettuando sostanziali investimenti per la produzione e la qualità, rivolge la propria attività al settore della componentistica ad alto contenuto tecnologico.
Intorno alla metà degli anni novanta, per rispondere alla crescente domanda dei propri clienti, l’azienda diversifica la produzione, integrando la finitura e la lavorazione meccanica dei propri prodotti.
Grazie ai continui investimenti nella qualità e la ricerca e alla collaborazione di personale esperto e qualificato, Pressofusione Saccense ha conquistato la fiducia dei propri clienti, diventando partner preferenziale di importanti aziende internazionali.
Con impianti tecnologicamente avanzati e ad elevato grado di automazione siamo in grado di produrre rapidamente getti pressofusi di precisione, spesso con caratteristiche specifiche in base alle richieste dei nostri clienti.
PROGETTO
Il progetto interessa principalmente 2 filoni: robotica avanzata e collaborativa, integrazione digitale nei processi aziendali. È iniziato nel 2017 ed è tuttora in corso con uno stato di avanzamento del 70%: parliamo, per esempio, della realizzazione di una nuova linea per un nuovo prodotto, arricchito da nuove fasi e KH prima esterni (verniciatura) o di staff (controllo qualità). Oltre all'integrazione digitale del nuovo processo, sta avvenendo anche una integrazione digitale del processo di gestione dell'energia, costruendo e consolidando internamente forti competenze legate alla installazione, misurazione, modellazione e simulazione del comportamento energetico delle macchine, processi e reparti. La progettazione è stata sia interna che esterna avvalendosi della collaborazione di alcuni fornitori I risultati attesi sono un aumento di produttività della nuova linea, un aumento della qualità dei prodotti realizzati, un sistema di indicatori e costing approfondito e aggiornato in tempo reale. L'investimento economico supera il milione di euro, comunque sarebbe stato attuato Gli strumenti relativi alle agevolazioni attività 4.0 (iperammortamento) o all'acquisto macchinari (sabatini) o alla ricerca e sviluppo (credito imposta) sono stati e sono utilizzati dall'azienda.
Vantaggi
Molto soddisfatto -la collaborazione con i colleghi a tutti i livelli, lo spirito di squadra e l'entusiasmo che il progetto è riuscito e riesce a coagulare -una proprietà lungimirante e solida che riesce ad avere non solo una visione di medio/lungo periodo ma anche uno stile di management quotidiano e concreto -la crescita delle competenze interne e professionalità legate alle persone -il realizzarsi delle attività e strategie previste, decise e condivise.
Svantaggi
Necessariamente l'esigenza (normale) di evadere gli ordini e le attività quotidiane, "il progetto 4.0" non sempre è percepito come indispensabile nell'immediato e a volte può essere ritardato (ma fa la differenza nel medio e lungo termine) le attività di rendicontazione e di agevolazione non sono agili e snelle.
VISIONE
- Inserimento di risorse in azienda in grado di portare valori ed energie nuove;
- approccio per processi, necessità di visione trasversale dell'azienda;
- sviluppo e investimento in attività e metodologie di project e program management;
- creazione di nuove figure o ruoli;
- coagulazione e consolidamento del reparto ricerca e sviluppo.
10 - AB ANALITICA
AB ANALITICA è stata una delle prime aziende italiane ad operare nel campo della diagnostica molecolare e ad oggi vanta oltre 25 anni di esperienza nella progettazione, sviluppo e produzione di diagnostici in vitro.
Un percorso lungo, al passo con la veloce evoluzione di questo settore, senza perdere mai di vista gli obiettivi che ci siamo dati per i nostri clienti: Innovazione, Assistenza qualificata, Sicurezza e Qualità certificata.
PROGETTO
Il progetto riguarda l'integrazione di aspetti afferenti a diverse aree aziendali - un sistema informatico per il Sistema Qualità aziendale nel settore dei Dispositivi Medici, integrato con il software gestionale ERP, con interfaccia utente ad alta usabilità e architettura allo stato dell'arte - un sistema per la gestione di magazzino integrato con il software gestionale ERP, basato su identificazione automatica e in grado di supportare attività eterogenee (produzione, rivendita, assistenza tecnica su linee di business numerose) - l'automazione della produzione e dei controlli di qualità di produzione Sono state svolte analisi, progettazione e attuazione con risorse primariamente interne e con il coinvolgimento di fornitori esterni su aspetti specifici. Il progetto è ancora in corso per le prime due parti e si è concluso per la terza, per la quale sono stati ottenuti i risultati di efficienza e tracciabilità previsti, con un investimento complessivo di € 140.000 e un finanziamento di € 5.000
Vantaggi
Per la parte già realizzata siamo soddisfatti del lavoro realizzato. Il principale motivo di soddisfazione deriva dalla constatazione che l'adozione di soluzioni 4.0 ha effettivamente determinato un salto di qualità nei processi aziendali che consente di far fronte alle necessità di crescita aziendale. Il progetto ha consentito di migliorare l'efficienza aziendale e la tracciabilità dei processi.
Svantaggi
Si è riscontrato come principale punto debole l'adeguatezza dei fornitori esterni alle necessità aziendali in termini di capacità di risposta ai requisiti di timing del progetto.
VISIONE
Il progetto ha permesso di migliorare l'efficienza aziendale e la tracciabilità dei processi. Inoltre ha permesso la crescita professionale dei dipendenti coinvolti su specifiche tematiche 4.0 e di sviluppare know-how interno utile alla realizzazione delle attività interne e al coordinamento di fornitori esterni in ambito Industria 4.0. In particolare l'azienda ha acquisito con attività sul campo la capacità di portare a termine diverse attività tra cui - l'analisi funzionale - la selezione tecnico-commerciale delle soluzioni e dei prodotti - l'installazione e l'integrazione - la configurazione - la formazione agli operatori.
I risultati e le ricadute del progetto vengono tenuti nella massima considerazione nella valutazione delle nuove scelte aziendali. Si prevede di poter scalare le soluzioni già implementate per rispondere ad esigenze di produttività superiore e di valutarne l'adattamento e l'estensione ad altre linee di prodotto.
11 - EPTA
Epta, Gruppo multinazionale specializzato nella refrigerazione commerciale per la Distribuzione Organizzata, si è affermata nello scenario mondiale, grazie a una solida cultura industriale, a una grande forza competitiva e alla significativa presenza del Gruppo sia in termini geografici, sia in numerose aree di business. Il Gruppo offre la più ampia e articolata gamma di soluzioni per la refrigerazione commerciale, assicurando la fornitura, l’installazione e la manutenzione di impianti, sia in modo diretto, sia avvalendosi di una capillare rete di distributori in tutto il mondo. Il Gruppo Epta opera attivamente anche nell’ambito del Food & Beverage, in qualità di partner di importanti player del settore. La vocazione di Epta si focalizza nella scelta di coniugare il valore dell’esperienza con le potenzialità dell’innovazione, con l’impegno a promuovere un progresso sostenibile e con la volontà di perseguire costantemente una strategia di internazionalizzazione.
PROGETTO
EPTA è una società in evoluzione continua e promuove, nei suoi stabilimenti, investimenti legati all'introduzione di nuove tecnologie o di rinnovamento. Da quando è in auge l'INDUSTRIA 4.0, si è prestata particolare attenzione al fatto che ciò che si introduce in azienda, corrisponda ai requisiti fondamentali per poter accedere alle agevolazioni previste e per godere dei vantaggi organizzativi che la digitalizzazione dei dati propone. In particolare, sono stati introdotti nuovi impianti di lavorazione lamiera e vetro e nuovi reparti di lavorazione dei tubolari in acciaio con tecnologia laser. Sono impianti progettati dalle ditte fornitrici sulla base di specifiche tecniche aziendali, basate principalmente sulla produttività e sulla flessibilità. Gli investimenti realizzati negli ultimi anni valgono svariati milioni di euro. In ottica produttiva globale, si sta affrontando un progetto specifico che prevede la digitalizzazione e la sincronizzazione dei dati di fabbrica che opererà in parallelo al sistema informativo aziendale, prioritizzando le operazioni di produzione, logistica e manutenzione.
Vantaggi
Gli investimenti proposti/realizzati, hanno dato risultati in linea alle aspettative (dato oggettivo certificato dal Controllo di Gestione). La soddisfazione, in azienda, viene misurata con dati economici; gli investimenti concretizzati hanno un R.O.I. (Return of investment) in linea con quanto ipotizzato.
Svantaggi
Ogni investimento ha un punto debole: nel nostro caso, il progetto di investimento viene calcolato basandosi su volumi produttivi proiettati negli anni futuri; nel caso in cui, i volumi fossero inferiori a quanto ipotizzato, il R.O.I. avrebbe un allungamento nel tempo.
VISIONE
L'influenza che l'Industria 4.0 sta dando all'azienda è rilevante: si stanno infatti attuando progetti che erano previsti più avanti, negli anni. È evidente quindi che il progetto sta dando una forte spinta a tutte le scelte aziendali. Le agevolazioni economiche permettono un R.O.I. più veloce, quindi è più conveniente investire e l'introduzione di sistemi di digitalizzazione in azienda, permette di avere una più ampia visione sulle Operations con uno snellimento dei processi aziendali.
12 - BERTI
La Berti Macchine Agricole S.p.A. nasce nel 1959 e rappresenta oggi una realtà leader nel mercato delle attrezzature per l’agricoltura e il movimento terra in Italia e all’estero.
La produzione comprende più di 500 modelli per garantire un’offerta assolutamente originale ed esclusiva capace di soddisfare a 360° le esigenze provenienti sia dal settore agricolo e della manutenzione del verde che quello del movimento terra.
Ogni anno l’azienda è in grado di introdurre sul mercato soluzioni interessanti e tecnologicamente innovative, presentate sistematicamente in occasione delle più importanti fiere italiane e internazionali
La ditta Berti ha sempre sostenuto, e sostiene, tenacemente il “made in Italy” dei suoi prodotti. Rispettando le attività lavorative della sua clientela al primo posto c’è la fermezza e l’orgoglio di assicurare qualità, affidabilità, durata e sicurezza nelle sue attrezzature.
PROGETTO
Il nostro progetto industria 4.0, non è nato come industria 4.0!
Avevamo la necessità di aumentare la produzione per non dover rinunciare a ordini. Abbiamo cercato un’area da fabbricare e, al momento di decidere quale fosse la superficie da coprire, ci siamo fatti supportare da società di logistica che, dall’analisi dei flussi dei materiali, hanno dimensionato la struttura e progettato i flussi. A questo punto ci siamo approcciati alla scelta degli impianti che nell’idea iniziale erano di tipo ordinario. Il beneficio fiscale dell’iperammortamento ci ha fatto uscire dagli schemi storici degli impianti, facendoci valutare l’opportunità di informatizzare la produzione. Qui si è aperto per noi un mondo nuovo, ma fin da subito abbiamo colto i vantaggi di una tale rivoluzione. Pertanto, si è proceduto con la progettazione della nuova struttura informatica in sinergia con le aree produttive e con i partner che avevamo individuato per gli impianti. Il progetto comprendeva l’inserimento di una linea di verniciatura robotizzata, un magazzino automatico e la tracciatura dell’avanzamento della produzione integrata con i collaudi intermedi. Le aspettative si sono realizzate e anche i più scettici hanno convenuto sul beneficio del grande investimento fatto. Circa il 50% dell’investimento è stato realizzato con un finanziamento Sabatini. Dalla progettazione è passato circa un anno e ad agosto 2018 siamo entrati nella nuova struttura con impianti in fase di start-up.
Vantaggi
Siamo molto soddisfatti del lavoro realizzato in quanto stiamo monitorando la produzione passo passo, abbiamo aumentato la qualità del prodotto e risparmiato sui tempi di esecuzione, soprattutto nella fase di immagazzinamento e prelievo dei materiali.
Svantaggi
Il punto debole è stata una sottovalutazione della fase di start-up degli impianti che ha richiesto delle energie molto superiori alle attese.
VISIONE
Questa nuova progettualità sta consentendo di recuperare informazioni dalla produzione che prima non si potevano avere se non con la presenza fisica di persone aggiuntive sulle linee. Il recupero dei collaudi just in time consente di creare i fascicoli macchina che poi possono essere gestiti automaticamente alla fine del processo produttivo. La gestione automatizzata del magazzino ci consente di ottimizzare i tempi di immagazzinamento e di spedizione.
Il progetto sta influenzando tutte le scelte aziendali, sia di investimenti futuri sia di procedure interne. Ogni iniziativa viene valutata nell’ottica di inserimento di un progetto unitario di informatizzazione globale. Sono partiti per i vecchi impianti revamping per adeguarli al nuovo sistema di fabbrica. Abbiamo già iniziato una ristrutturazione di spazi ed impianti dei vecchi stabilimenti per l’adeguamento ai nuovi standard, il processo di ultimerà nei prossimi tre anni. Tutti i nuovi impianti/attrezzature saranno per la maggior parte interconnessi con il sistema di fabbrica.
© RIPRODUZIONE RISERVATA
Riproduzione riservata © il Nord Est